And how does a custom builder help make better production bikes?
Tom Kellogg - a name that may jump out at you, some familiarity. Maybe you’ve heard of Spectrum Cycles. And you’ve most definitely ridden a product that Tom was instrumental in developing - having been behind the development of some of the first modern Titanium bikes and the development of modern carbon bicycle forks. Tom’s influence in cycling is greater than many know.
What does that have to do with Ritte? Through some luck, some friends, and some family we became acquainted with Tom back in 2019. He was getting ready to close up shop after some 40 years of building custom metal bicycles and advising on countless production models for the likes of Merlin, Seven, Time, and others. We were ramping up to build new steel models, wanting to offer the best production bikes we could without compromise.
Together, we took our big ideas and Tom’s guidance and experience into the Phantom and Satyr models. Tom helped us shape these bikes into something special - distilling as much of the DNA, ride experience, and construction quality of a custom built bicycle into two models that were ready to ride.
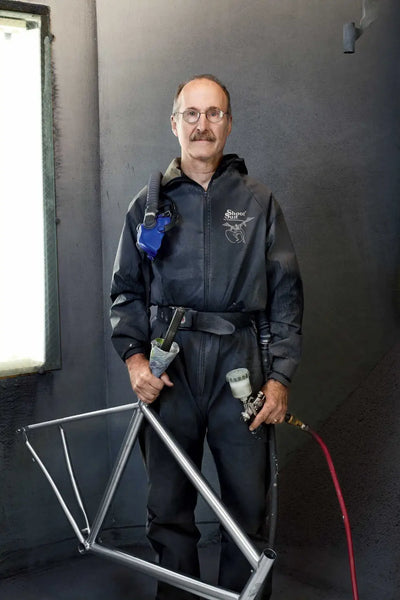
Tom’s decades of building not only world championship winning bikes, but bikes for normal folks across an enormous background and size range combine to give him the knowledge and expertise that few others can match. Tom’s expertise translates into the best metal bikes Ritte’s ever built - knowing exactly what it takes to make each size just right for the widest range of riders.
While there is no replacement for a custom bike, and we’d certainly never suggest as much, Tom had seen the whole gamut and knew how to take our desired ride qualities and translate them into bikes that work beautifully for most riders. There will always be a small percentage of people for whom custom is the only option, and some for whom it’s the desired option.
But for many, a ready to ride frameset is going to fit wonderfully - and that’s where we’ve looked to bridge the gap between what production steel bikes had been and what custom steel bikes can offer. Everyone deserves a bike that rides well, fits well, and makes cycling fun - in working with Tom we’ve been able to produce bikes that we feel fit that ethos and are available without a wait or the cost involved in going fully custom.
Our Phantom and Satyr steel-framed bikes come in 6 stock sizes with each being tailored to have the same desired ride quality. While most bikes come in a range of sizes, where these differ is having the hands on approach of fitting thousands of cyclists to custom made bicycles - Tom’s experience provides guidance here that cannot be replicated any other way. A small tweak can make a huge difference in keeping the ride feel and temperament of a bike consistent for riders of all sizes. Rather than take the tack of simply creating broad, even steps between sizes we’ve sought to make bikes that are tailored around how people themselves scale - are 60% of people within a certain height range? In that case, we’ve created smaller jumps between sizes for a more precise fit within that range.
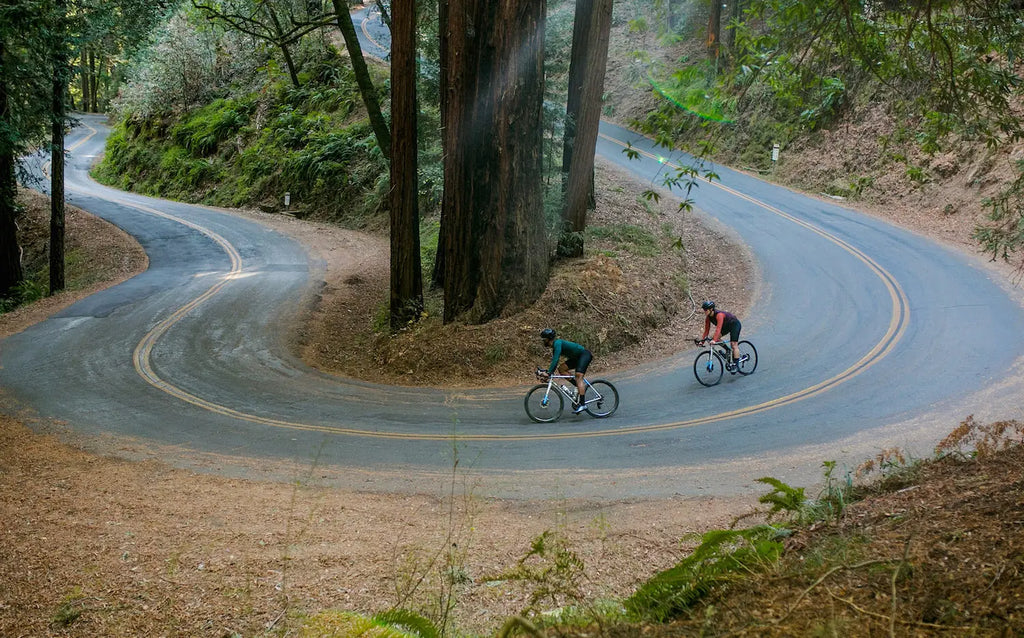
We’ve also worked to take some of the steps of building a custom bike into the production fray. Where a builder might select a tubeset just for each rider, we’ve done the same in designing and refining a tubeset that’s size specific. Outer diameters, wall thicknesses, and butting profiles all change based on the frame sizes. The same approach with geometry - where a factory built bike may prioritize cost savings over the most perfect geometry we’ve made the decision to go rider first. We size and shape all the chainstays for each frame, utilize forks of just the right rake (want to find out more about that? Check out our Geometry and Handling article), and more.
And where a custom builder may select a more involved production method or welding setup, we’ve followed suit. Whether it’s a specific process or specific TIG welding rod, we’ve chosen the setup that results in the highest quality and longest lasting bike. But, some aspects of production manufacturing allow us to go a step beyond what can generally be done in smaller custom builder facilities.
With a production level build we’re able to have all of our bikes ED / electrostatic anti rust coated - this is a full submersion coating process that protects our frames inside and out prior to being painted. There’s no need to worry about tearing bikes down and applying framesaver. And, with modest volume we’re able to do things like machine bottom brackets with extra clearance for internal routing and have headtubes turned that are perfectly matched to our fork crowns and taper specifically with each size of frame.
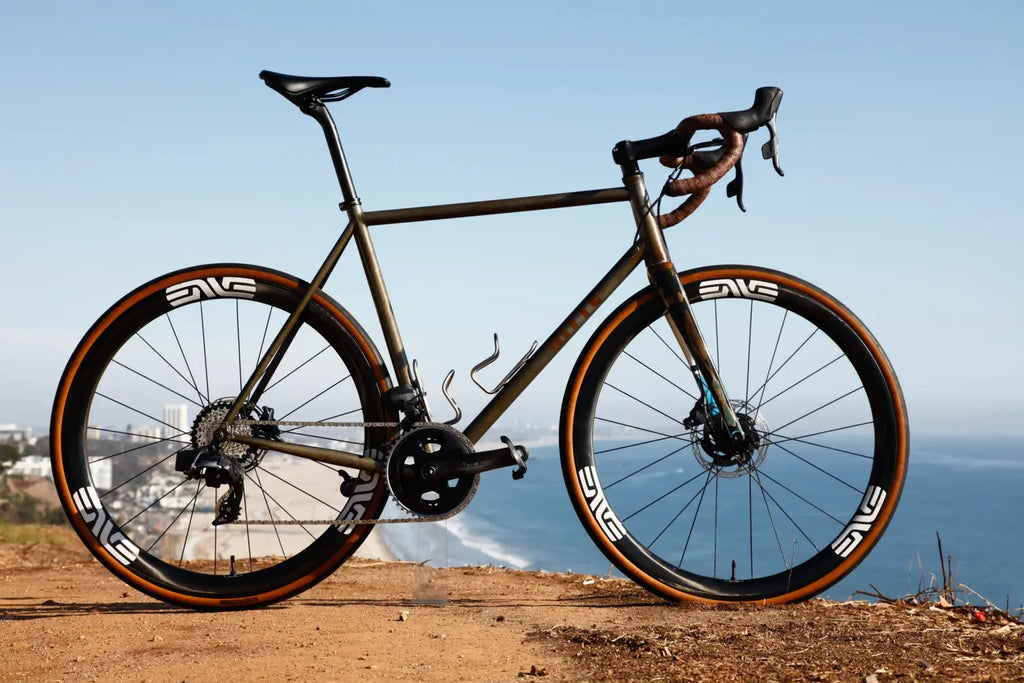
Since Ritte’s inception, we’ve always looked to have fun with our paint and apply quality finishes that look great for a long time. These steel bikes are no different, and we’ve worked hand in hand with our painters to create something we’re proud of. We also offer ready-to-paint finishes on all of our frames if you’d like something custom - and those ready-to-paint finishes still include our anti-rust treatment so your painter (or ours) is ready to rock.
Working with Tom Kellogg has given us the ability to get the best of all worlds - from ride quality, geometry, and tube specification through to construction methods and finishing. We’ve been so fortunate to combine the strengths that we each bring to the table to build what we think are some of the finest metal bikes on the road.
For those that do want a fully custom ride, see our Made in US titanium bikes - a further collaboration with Tom Kellogg on some very special made to suit road and gravel bikes.